Back in March, I was contacted by Amanda McClellan of Coordinate It wedding planning. She’s interested in LED lighting for paper party lanterns; and although she has an engineering degree, electronics is not specifically her forte. She wondered whether I help her figure out how to drive the LEDs, and, well, you know how I feel about LEDs.
So of course I was interested.
The challenge, of course, is that LEDs need a constant-current drive; and it’s not easy to drive a string of LEDs at a constant current (hence constant brightness) using a simple current-limiting resistor. I’ve looking at constant-current LED driver ICs, and am close to putting together a simple but useful LED driver circuit, with intention to both open-source the design and offer the hardware for sale. More on that soon.
LED Tester
Meanwhile, as I’ve researched driver chips, Amanda and I have been talking about how many LEDs (and indirectly how many mA) it takes to light a paper lantern. She wants the lanterns for decoration, not illumination — Last weekend I assembled and shipped her a simple LED tester to allow her to try some LEDs inside lanterns and see how many LEDs and how much current she’s going to want.
My idea was to make something that could:
- run off a 9V battery (enough to power a series string of two white LEDs at ~3.4V each)
- allow her to vary the LED brightness for testing
- allow her to measure the LED current without having to stick an ammeter in the circuit
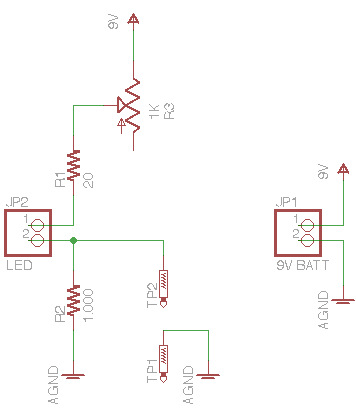
Regarding that last point — ammeters have to be connected in series with the circuit under test, so the LEDs would go dark when the meter wasn’t connected. Instead, I used a 1.0Ω current-sensing resistor in series with the LED string. Across the 1Ω resistor one can measure 1mV for each 1mA of LED current; and removing the voltmeter from the circuit has no effect on the LED operation.
R1 (20Ω) is there to save things if the potentiometer is turned to its minimum value of (theoretically) 0Ω. With two 3.4V LEDs in series, the combined LED voltage drop is 6.8V and the voltage remaining across the various resistors is 2.2V (or .4V with the NiMH “9V” battery I use at home). 2.2V / 21Ω ≈ 105mA, which is way too high for a normal LED and puts almost a quarter watt across R1. Not great; but it’s a last resort instead of a dead short, not a desired operating mode.
The Board
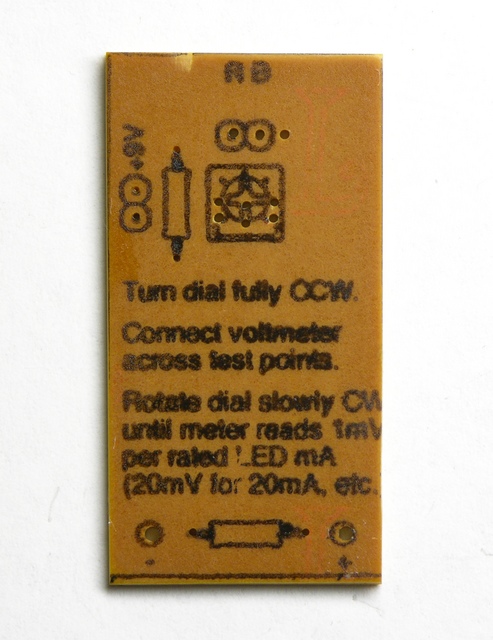
I used the laser printer and household iron to do toner transfer for etch resist, and also to transfer the “silkscreen” on the top side. I get best results on the silkscreen side peeling off the paper while everything is still hot, and I was particularly pleased with the transfer quality here. Not perfect, but it’s pretty legible for 70-mil text.
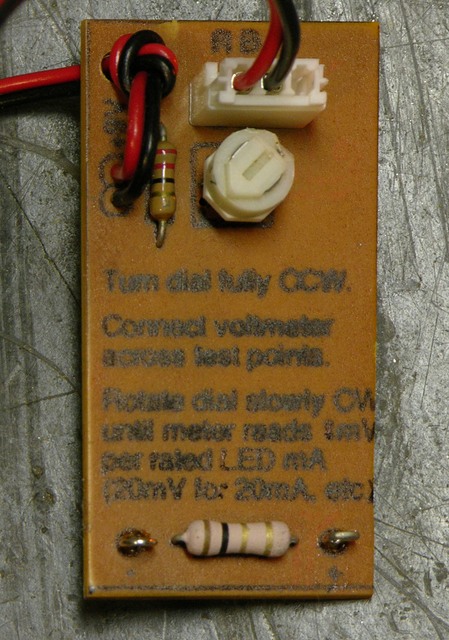
Here’s the populated board, sized the same as the battery it runs from. In retrospect, I should have moved the potentiometer further down or the LED connector further up, but I was intending to use a right-angle connector that would lay flat on the board. Couldn’t find any in my parts bin when I went to assemble it.
The test points at the bottom are wire loops sized to friction-fit my voltmeter probes. They’ll also work well for clips or gator wires.
In Use
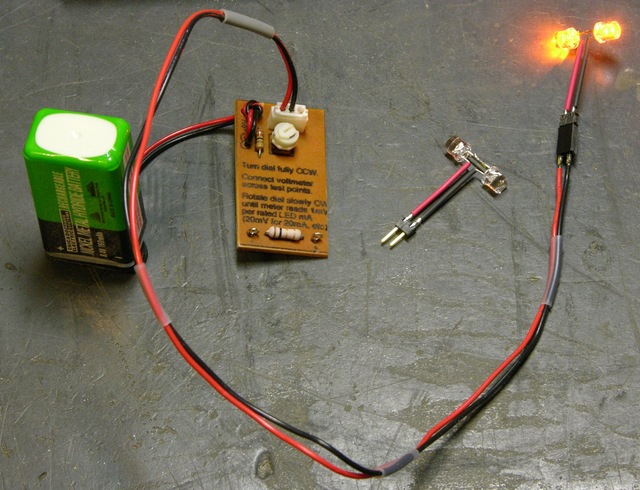
Here it is in action with a couple of amber LEDs plugged in. They don’t look bright enough to me — but letting Amanda determine that is the whole point of this exercise. She’s the expert on event planning; and it’s her assessment that matters, not mine.
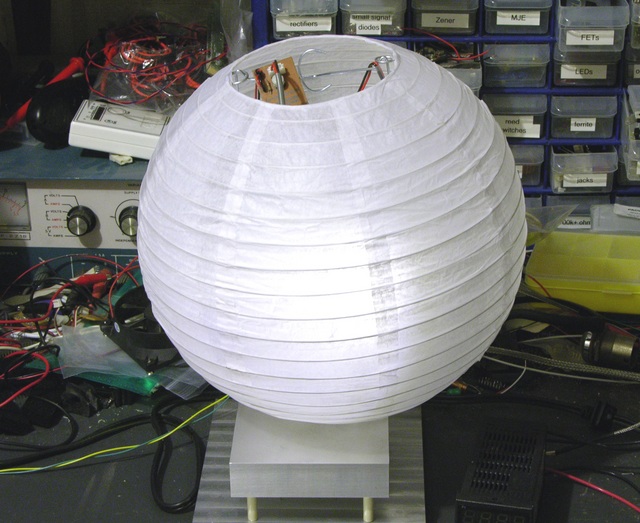
This is two warm white LEDs inside a paper lantern. Under normal room lighting, you can tell there’s light inside, but it doesn’t look dramatically lighted and diffused as I think one would want it to.
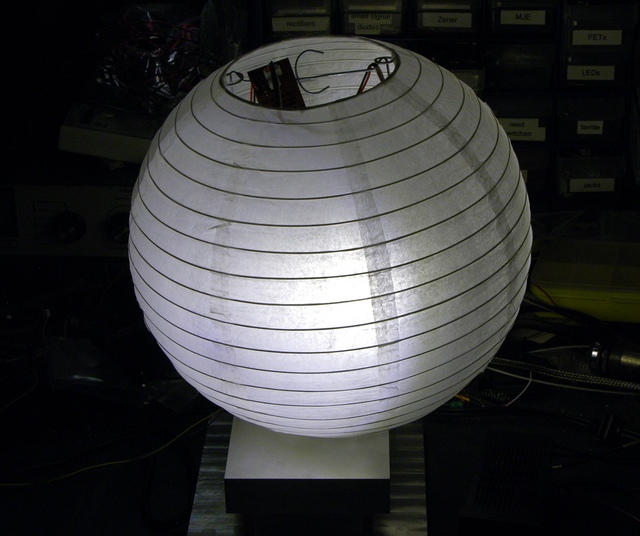
In evening darkness, the lighting is more noticeable. And in spite of having set white balance carefully before taking the shot, my old camera changes the warm yellowish white light into cold blueish white light. Ach, what can a fellow do. Looks good in person, though — if not necessarily bright enough (to me).