Last fall I bought a used InFocus LP290 projector, and in January I opened it up and found that the polarizing filter for the blue LCD was melted. Since then I’ve been keeping an eye out for a replacement filter, and Monday night I parted out a dead Optoma projector from Jeremy for the polarizers. Tonight I fitted one to the InFocus, with surprising success.
LCDs and Polarizing Filters
A long time ago, I think I knew how LCDs work, but I’d forgotten until a great conversation I had with Dave, who posts comments here from time to time and is immensely knowledgeable about LCDs. To paraphrase:
In high school physics, we learn that light behaves as both particles and waves (both of which can be demonstrated experimentally). In the wave model, light is a transverse wave: it “wiggles” from side to side in a plane containing its line of travel. (In contrast, sound is a longitudinal wave — it makes compressions and rarefactions back and forth only within the line of travel.)
Normal light has waves wiggling in all directions around the line of travel — up and down, side to side, and all angles in between. A polarizing filter only lets through light waves wiggling in one particular orientation, say up and down. It also lets through the up-and-down component of waves wiggling at an angle other than up and down; but waves wiggle side to side have zero up-and-down component and get completely block.
Digression: polarizing filters are used in photography and in sunglasses to block glare. It turns out that the light waves in certain kinds of glare have been polarized by their reflection off the surface of whatever object is glaring, and polarizing filters can completely block those types of glare. It’s a really cool effect to rotate a polarizing filter in front of something that’s backlit at a fairly steep angle and watch the glare appear and disappear.
I have this description backwards. See Dave’s comment for an excellent description of how it really works.
Back to LCDs: the crystals in LCDs pass light waves untouched when they’re inactive, and twist the polar orientation of light waves when active. This is the key to how LCDs work.
An LCD screen like on a cheap calculator has a polarizing filter in front, the LCD panel, and a backing mirror. Light from the room hits the filter and only the portion in the proper orientation (say up and down) passes through. That light then passes through the LCD, and where the LCD is inactive the light maintains the same orientation. It reflects off the back, passes through the LCD untouched again, and is already in the correct orientation to pass through the polarizing filter on the way out. Thus where the LCD is inactive, you see light areas.
Where the LCD is active, it twists the polarization of the light waves by 45°. (There are other possibilities, but I’m talking about simple and cheap.) It reflects off the mirrored back and passes through the LCD again, getting another 45° of twist for a total of 90° with respect to the polarizing filter. That’s exactly the angle of polarization that’s completely blocked; so where the LCD is active, you see dark areas.
In projectors, with light passing through the LCD only once, it has to work a little differently. I’m guessing the LCD does 90° of twist, with polarizing filters both before and after.
So without the “before” polarizing filter in the blue light path of my projector, the darkest the blue beam could ever be was about medium-bright, because it only got half as filtered as it was supposed to. Instead of true blacks, I got medium blues. White was still white, of course, because that’s where the light was supposed to pass through (and still did).
Colored Polarizing Filters
Looking at the optics inside projectors, there are lots of things reflecting, refracting, and filtering light, and I often see color tints and have trouble determining which thing I see is the color filter. So after taking the first polarizing filter off the Optoma and finding it to be a dark blue-grey, I thought it was a neutral grey and didn’t think any further about color.
Tonight I found that each polarizing filter is a different color, complemenrary to the color of the light path it’s installed in. I was having trouble figuring out why you’d want to have a color filter and a polarizer. Since the yellow-orange filter blocks blue light in the blue beam, it seemed it would simply dim the blue beam all around. Okay, that leads to blacker blacks; but (apparently) in the same way as just using a dimmer bulb. That didn’t make any sense.
Then I looked through the colored polarizing filter more carefully.
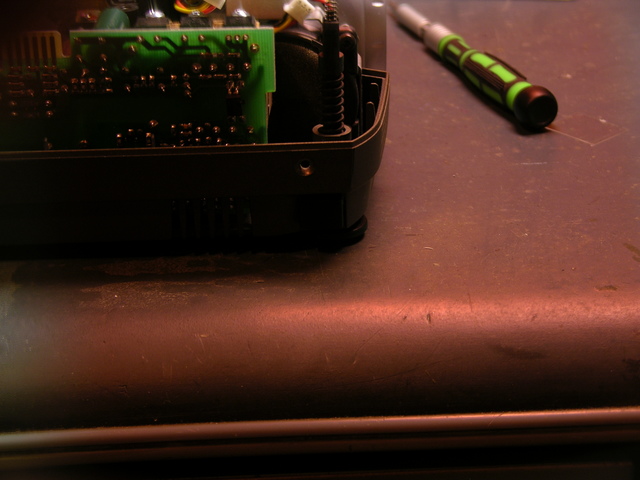
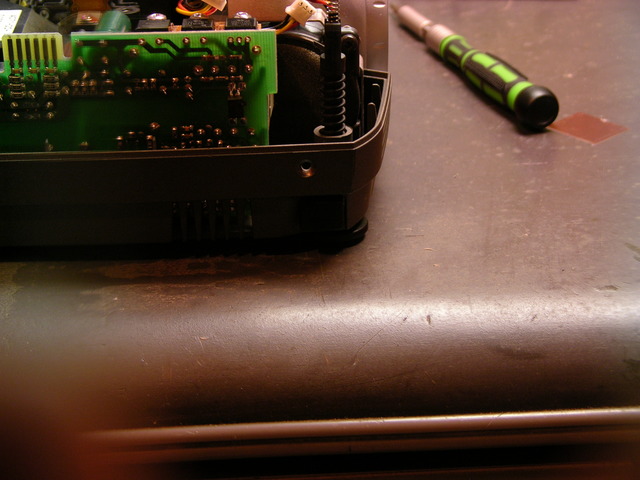
The two pictures are taken with the same camera settings, the first with the orangey filter held in front of the lens horizontally, the second vertically.
Both pictures have the orangey cast to them, but notice in particular the color of the glare on the edge of my desk. In the second picture, it’s nearly white, not orangey like everything else. That’s where the glare is.
I believe this filter passes all colors of light in general, and specifically blocks blue light that has opposing polarization. That’s why the screwdriver looks about the same in both pictures — everything except blue gets through, and the light from the screwdriver isn’t polarized so the blue is blocked. The glare on the edge of the desk is polarized, so even the blue gets through and gives a more even white.
That’s kinda cool. And that means the filter should do an extra good job of darkening blues where the LCD is active. With a complementary-colored filter in each of the three color beams, it means it should do a really good job of making black blacks.
Fitting the Filter to the Projector
The InFocus and Optoma obviously don’t use the same size filters, as the Optoma filter clearly doesn’t fit the InFocus carrier. Fortunately, the Optoma filter is larger, so at least I can hack it to work.
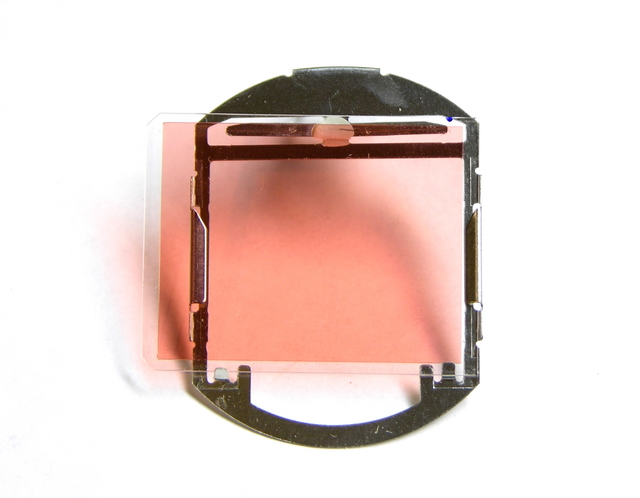
(The camera doesn’t represent the filter color very well, by the way. In real life, it looks very similar to the deep orangey-yellow of yellow liquid food coloring, not as pink as it looks here.)
I confirmed the proper orientation for the filter by very carefully slipping it into position in the projector and holding it there with a needlenose pliers with the projector running, and the proper orientation is horizontal. Too bad, since the Optoma filter was as tall (short dimension) as the InFocus carrier is wide (long dimension), and it actually fit really well in the carrier the wrong way.
But with a little bending of the carrier edges, I got the too-large filter secured in (and hanging out of) the carrier well enough to reassemble the projector. The glass isn’t parallel to the carrier any more, but I can’t think of any reason that’ll make a difference. You can see the glass slide sticking too far to the left, and slanting forward, in this picture, between the silver carrier mounting tab above and the LCD housing below.
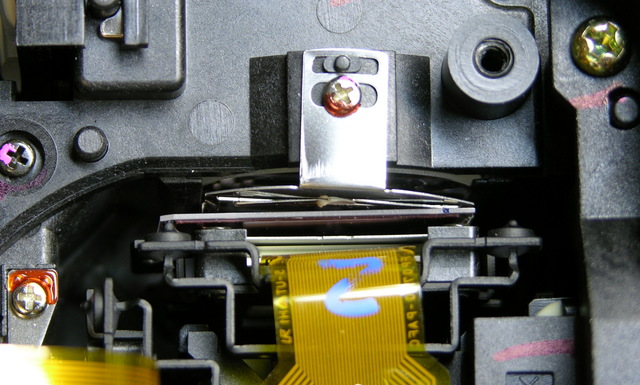
The projector works now, and the blacks are black again! I’m not ready to close it up and call it done until I sit next to the projector and test it for an evening to make sure it’s not going to melt down and light my house on fire, but I’m optimistic. And if it works, I’ll think about cutting down the glass the filter is mounted to, so it fits properly.