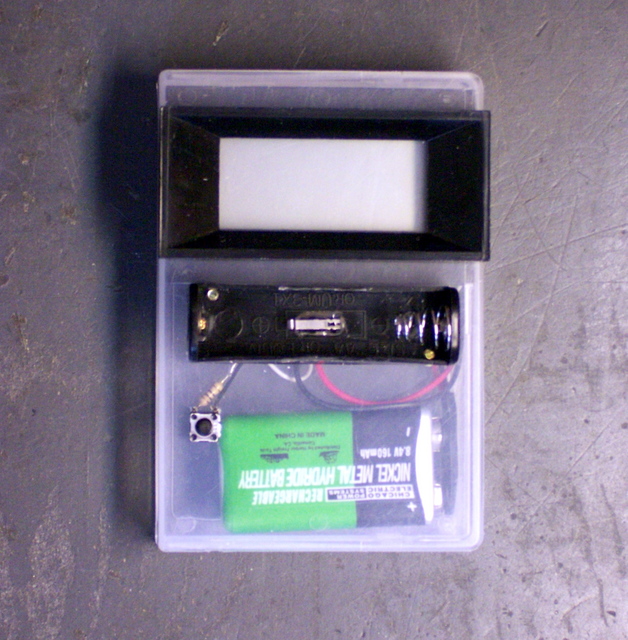
Here’s a project that I’ve been kicking around for a long time (three years–I guess that’s not so long compared to some of my projects
) and finally built–a battery meter. My friend/enabler Slim Cummings in Pittsburg gave me a couple of surplus 3-1/2 digit, .2V panel meters, and I thought they’d be perfect for testing the freshness of AA and AAA cells.
Meter
The meter was the inspiration for the project. It has a 3-1/2 digit (a 1 plus three 7-segment digits–1888) display, a configurable decimal point, and an Intersil ICL7106CPL LCD/LED Display, A/D converter chip. You give it 9V supply, a jumper for the decimal point, and a voltage input; and it samples the voltage and drives the LCD. It’s a very nice package that just begs to be used for something interesting.
Tester Case and Battery Holder
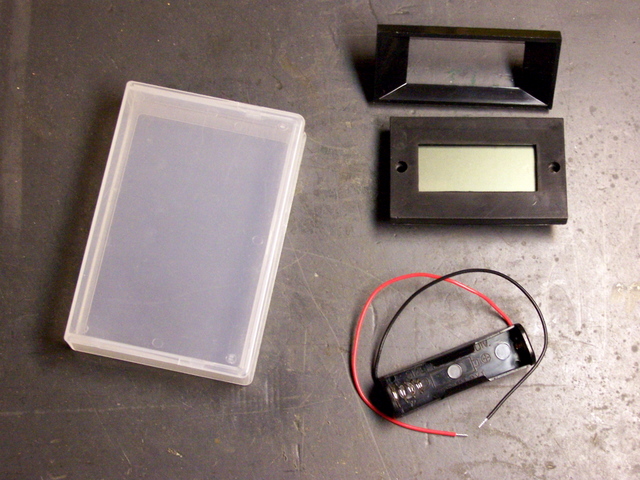
The physical aspects of the project actually took much longer than the electrical. First off, I wanted to find a case with the following characteristics:
- The case would be held in portrait orientation.
- The meter would fit across the width of the case, with the battery holder below it.
- I could fit a 9V battery inside the case to power the meter.
I figured I’d find a plastic project case from Radio Shack with a 9V holder in one end and enough room for everything else to fit . . . no such luck. I figured I’d find something in my junk bin that I could reuse–I was coming close with some old and broken copper-to-fiber media adapters, but they weren’t quite right. Finally I stumbled across the idea of using the plastic case from a data backup tape, and I rummaged around until I found this KAO 8mm data cartridge case.
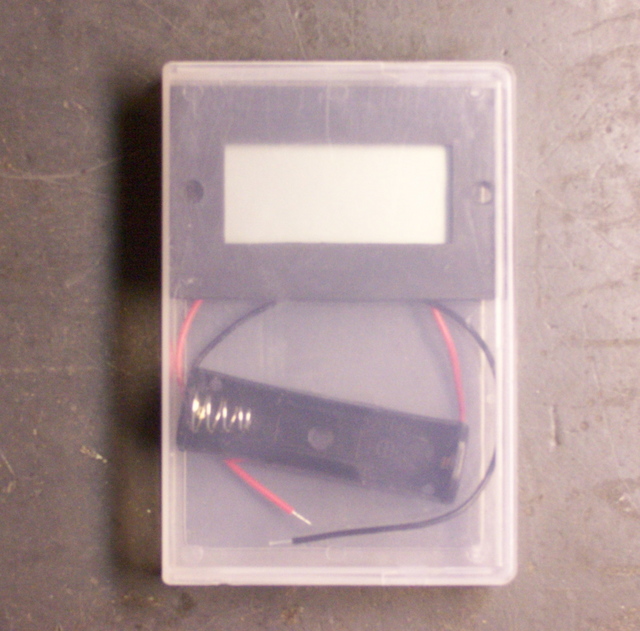
I’m not wild that it’s translucent–I don’t like seeing the guts of things when I’m using them–but it’s the perfect size. The meter exactly fits across the width, the 9V battery exactly fits in the thickness, and it’s in portrait format. Plus I guess it’s kind of cute opening the case like a cassette case to change the 9V battery.

I picked up a single AA battery holder at Radio Shack a couple of weeks ago, and had to mod it a bit to fit it onto the case the way I wanted. The leads originally routed out holes in the ends of the holder, but I wanted them to go straight down through the case. Fortunately, there was already a hole underneath the terminal at each end (you can see the one at the right end of the above picture), and I was able to fish the wires through and tug them into position to make it work.
The holder also had tabs curving slightly around the front, to help hold the AA cell inside. Since I want to be able to insert and remove cells quickly, I removed the tabs by scoring the plastic flush with the rest of the front of the holder, then snapping them off. I also confirmed at this point that a AAA cell would make contact with both ends of the holder, even though it wouldn’t be held as securely. (AAA cells are shorter than AA cells, as well as thinner.)
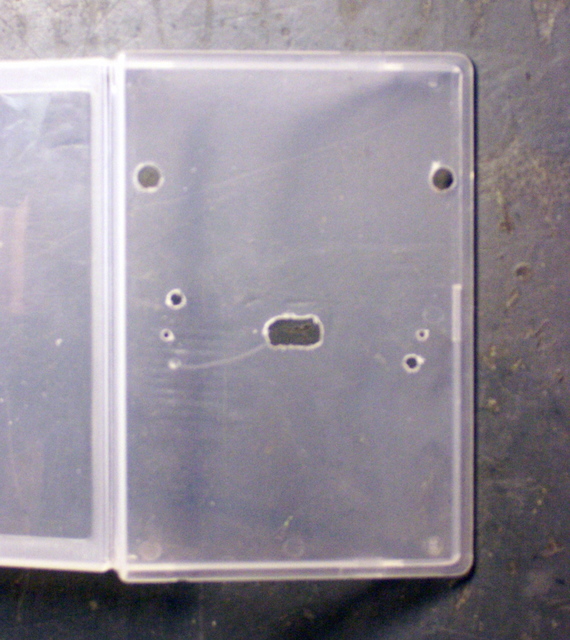
I drilled mounting holes in the case for the meter and battery holder, as well as holes for the wires to go through. The plastic was so soft, I didn’t even bother chucking the bits into my drill for most of the holes–I just turned the bits a few rounds with my fingers and I was through the case.

I did get to use my stepped drill bit set to enlarge the meter’s mounting holes–the bezel’s posts have larger-diameter plastic shoulders at the base, my mini-drill doesn’t have bits that large, and the stepped drill bits do an excellent job of enlarging while remaining concentric with the pilot hole.
The last tricky bit of work with the drill was the big ugly hole in the center of the picture of the drilled case. I needed a power switch for the meter, but I was loath to have to have to slide a switch or press a button every time I wanted to use it–I wanted it to spring to life when a cell was inserted to test. Plus for reasons to be described a bit later, I planned for a pushbutton on the front already, and I didn’t want to have two.
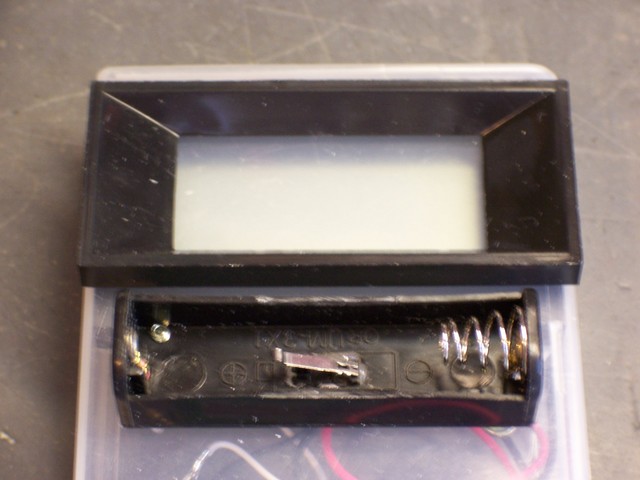
The solution was simple enough–a pushbutton switch inside the battery holder, actuated by the insertion of the cell itself. I salvaged a tiny microswitch (“nanoswitch???”) from a dead CD-ROM drive (a limit switch from the optical sled), reamed much too large a hole in the case and battery holder, poked the switch in from underneath, and hot-glued it in place.
Meter Wiring
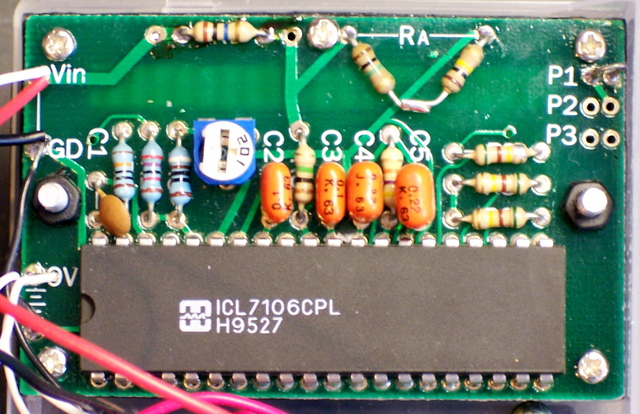
The meter board is built for a range of 0 – .1999 (.2) V, but has pads to set the placement of the decimal point and to provide your own voltage divider to adapt for other ranges. The documentation gave the resistor values to adapt for 20V and 200V, from which it was easy enough extrapolate the nominal values for 2V operation: 9MΩ and 1MΩ. Well, I have 1MΩ resistors on hand, but not 9MΩ, and certainly not precision.
Fortunately, 9:1 ≅ 10:1.1, so I put a 10MΩ resistor into the pads for RB (upper left) and chained a 1MΩ and a 100kΩ in series between the pads for RA. (Those lap-soldering skills from a summer of module assembly at IFR Systems do come in handy.) Also fortunately, the calibration potentiometer had a generous range, so I was able to work around the 1% difference from the nominal ratio.
I also guessed (correctly) that the proper position for the decimal-select jumper was P1, which was missing from the voltage range chart.
Assembly
I had one more set of components to add, but I couldn’t resist wiring it up to see how it worked so far.
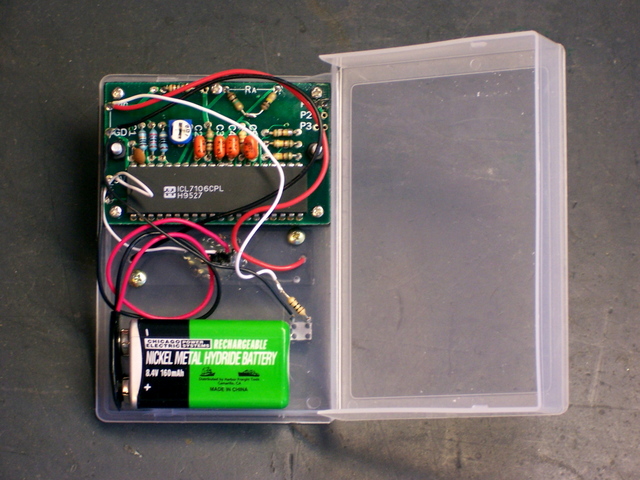
I soldered the 9V battery clip’s ground lead to the ground connection at the lower left of the meter board, the positive lead to the microswitch glued into the AA holder, and the normally open (NO) lead from the microswitch to the supply connection on the meter. I also soldered the AA battery holder’s leads to the Vin connections at the upper left. If you look closely enough, you may see that I just tack-soldered them in place with a lot of exposed wire a the end; I plan to come back and organize the wiring more carefully, and didn’t take a lot of extra effort at this point.
Meter in Action
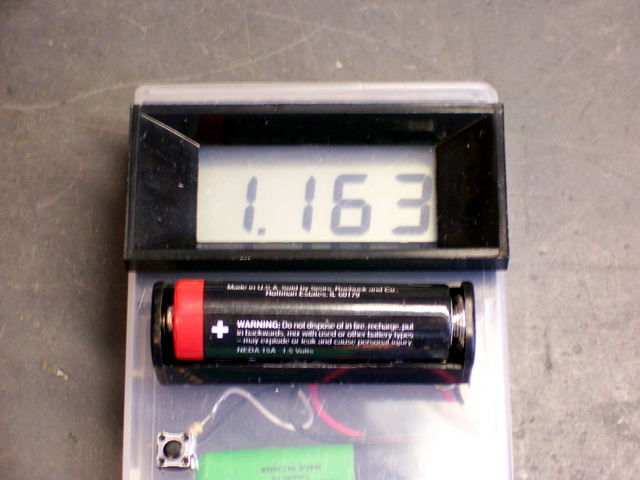
And it works as planned! Not that there was much surprise, but it’s still nice when a project comes together. I was also pleased that the (undocumented) position of the decimal point was correct. Further, I was hoping to avoid cutting a large hole in the box for the panel meter; and I find it adequately legible reading through the nearly transparent case, without a hole.
I put a AA cell into the holder, the switch activated beautifully, the meter sprang to life, and I had a reading of the AA cell’s voltage. I measured the cell’s voltage in situ with my best voltmeter, calibrated the panel meter’s reading via the potentiometer on the back, and measured with my good meter once more to make sure the voltage hadn’t drifted while I was adjusting. Good enough!
Load Testing
Finally, I drilled two more small holes in the case, poked a pushbutton switch through (in the lower left of the above photograph), and wired a 10Ω resistor in series with the switch, and the switched resistor in parallel with the AA holder. From my first inspiration for this project, I’ve wanted to be able to test cells under load as well as unloaded. I find that some cells I’ve owned–particularly, I believe, when they’ve lost capacity due to age rather than use–will show a relatively high unloaded voltage even though they have very few mAh left. I very specifically wanted to be able to test under load to identify this condition.
And it’s proved itself already. The cell shown under test reads 1.163V, which is by no means new, but might still appear to be usable in some types of devices. But when tested with a load, it drops immediately to ∼.8V and continues to fall toward .7V–not nearly as promising. In contrast, another cell I’ve tested measured ∼1.2V unloaded, but still ∼1.1V under load–very likely quite usable yet.
Sorting Batteries
I’ve already switched to using NiMH cells for all my projects and consumer hardware, but I have a number of alkaline AA and AAA cells around the house from the old digital camera and the Visor PDA, with no good idea which are fresh and which need to be discarded. (Y’know, it’s such a pain to test cells with a voltmeter and only two hands.) I can finally conveniently test and sort them into four categories:
- Unused: Save for when I don’t have any rechargeables ready, or give with battery-powered gifts to nieces and nephews who don’t do the whole “rechargeable thing.”
- Still strong: Save for my LED flashlight, which seems to get quite a bit more life out of used cells than do incandescent lights.
- Weak: An interesting problem. They still have some energy stored, but not enough to use in traditional portable devices.
I’m planning to build a “Joule thief,” a clever and tiny transformer feedback single transistor inverter that claims to be able to “provide a week of continuous low level light from a battery that would normally be considered dead.” Maybe I’ll end up with a bunch of “electronic candles” sitting around for the next ice storm; who knows.
Update: Here’s another Joule thief project.
- Dead: Take to work and toss into the battery recycling bin. (And scrounge “weak” cells out of the bin to take home and make more “candles,” har har! Just don’t tell my wife that I’m stealing other people’s dead batteries now . . .)
Credit
A huge thank-you to my friend Slim, who gave me the panel meters that started this all; and who’s always generous with his vast experience and equally vast stores of electronics surplus.