A couple of weekends ago I took the two XB-2s that I had (at the time) over to Ron’s shop to have a little more room to spread out and test things. Like real Hammond tonewheel organs, the XB-2 has “drawbars” that represent different harmonics (or subharmonics) of the fundamental frequency of each key being pressed; you draw out the bars to mix different amounts of the different harmonics to get the timbre you want. This is additive synthesis at its most visceral.
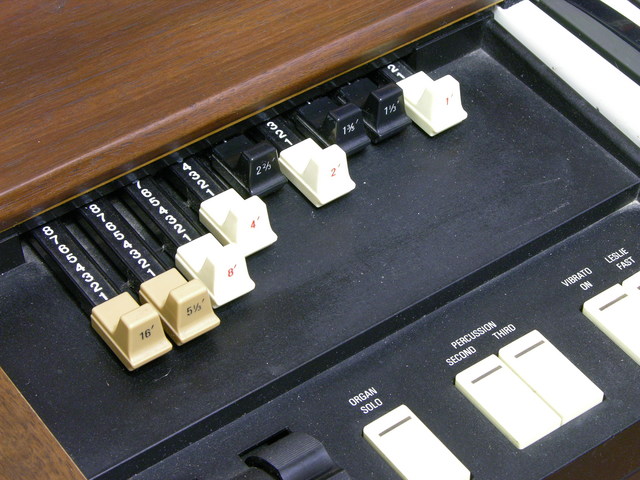
On the XB-2, the drawbar positions (either live or recalled from memory) are displayed on an LCD below the manual (keyboard). In live mode, the bar graphs move in and out in synchrony with the physical drawbars.
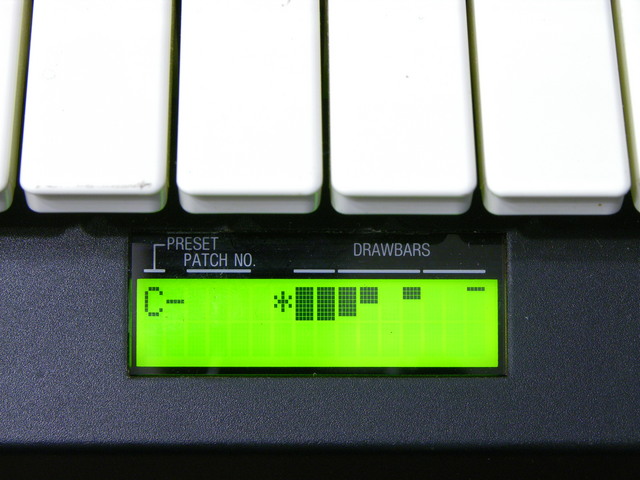
On one of the two XB-2s, the LCD bar graphs didn’t match the drawbars — a couple of drawbars appeared to work properly, but some didn’t work at all and others moved multiple bar graphs on the display. Since the drawbar decoding is a relatively independent section of the organ, it seemed like an easy repair to tackle first.
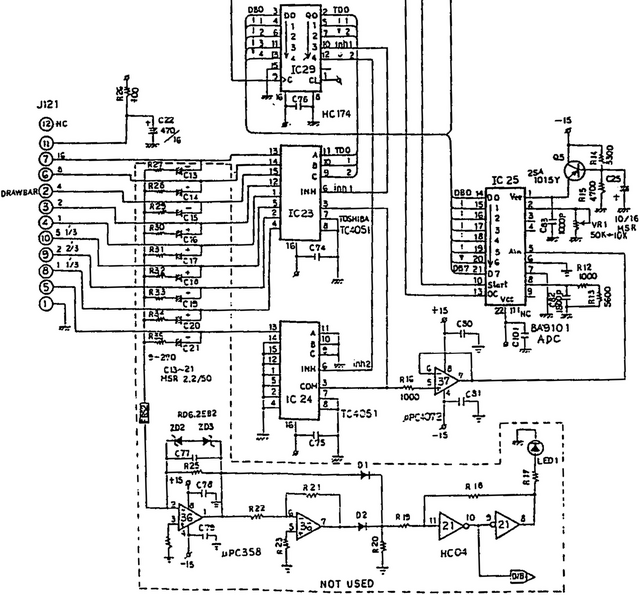
The drawbar’s wiring harness plugs into the main board on J121, at the left of this section from the service manual. Each drawbar is a detented slide potentiometer, so variable voltages are arriving on J121. The section enclosed in the dotted line and marked not used truly isn’t populated on the circuit board, so I omit it from discussion.
The nine analog drawbar voltages are delivered to IC23 and IC24 (TC4051 analog multiplexers). The multiplexers receive their enable and select signals from the output of IC29 (74HC174 hex D flip-flop) which is latching signals previously delivered from the system data bus. (In other words, the 74HC174 is the drawbar select register; its own address is decoded elsewhere in the schematic.)
The chosen (enabled) TC4051 analog mux selects which input to pass to its output on pin 3, which is then op-amp buffered and delivered to the input pin of IC25 (BA9101 analog-digital converter). When selected (more system address bus decoding), the ADC writes the digital value of the drawbar’s position onto the system data bus.
Side note: For the drawbars only having nine detents (0-8), IC25 sure delivers a lot of bits of ADC resolution to the data bus.
I put a scope on IC23 (analog mux)’s output pin and I was able to view on the screen the time-division multiplexing of the drawbar positions (analog voltages) onto the single line going to the ADC. It mostly matched what I saw on the LCD, although there were some quirks with a few of the drawbar time divisions appearing narrower than others. Ignoring the odd widths and recording which drawbar occupied which time division:
Drawbar Time-Division Multiplexing Behavior
|
Drawbar |
16 |
8 |
4 |
2 |
1 |
5 1/3 |
2 2/3 |
1 1/3 |
1 3/5 |
IC23 Pin |
13 |
14 |
15 |
12 |
1 |
5 |
2 |
4 |
(IC24) |
IC23 Input |
Good MB |
0 (000) |
1 (001) |
2 (010) |
3 (011) |
4 (100) |
5 (101) |
6 (110) |
7 (111) |
(IC24) |
Bad MB |
0 (000) |
1 (001) |
7 (111) |
7 (111) |
0 (000) |
1 (001) |
7 (111) |
7 (111) |
(IC24) |
On the working XB-2 motherboard, the drawbars were selected and sampled in numerical order. On the broken motherboard, as you can see, any time the analog mux’s select bit A1 was enabled, the mux behaved as though bits A2 and A0 were enabled as well. Further, select bit A2 didn’t work on command as it should when drawbars 4-7 should have been chosen.
4051 Address Pins
Name |
C |
B |
A |
Function |
A2 |
A1 |
A0 |
Pin |
9 |
10 |
11 |
It could be a bad 4051 mux; but as we had already replaced a leaky electrolytic capacitor in the neighborhood, it seemed worth another look at the circuit board first. The 4051′s select lines are on pins 9-11, and what’s this?!
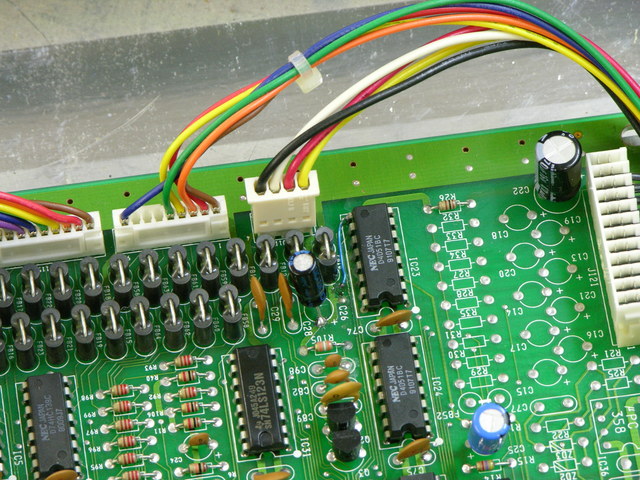
I became suspicious of a damaged via on a trace that turned out to connect to pin 9 (A2). A continuity test showed that the via — even its top side — was no longer connected to IC23; the trace up to the via had been eaten away by the leaking capacitor. The via — even its top side — did have continuity to its next stop on the PCB, so the via itself was intact.
Ron heated the solder that had wicked into the via during reflow, inserted a piece of wire-wrap wire, and soldered the other end directly to IC23 pin 9. The drawbars now work perfectly. I suspect the floating select input on the CMOS mux was picking up enough signal from the PCB trace inductively coupled to its neighbor to trigger.
My hypothesis is that the previous owner put the keyboard away because of larger (ROM / CPU / Muse) problems; the capacitor leaked and damaged the drawbar multiplexer trace while it was sitting idle; and the owner never even knew about the drawbar problem. At any rate, it was easily fixed and the troubleshooting was a rewarding mental exercise.